1. 引言
种子的称量、包装和物流是农业生产过程的重要环节 [1] 。而种子的包装,要按包装要求进行准确称量。称量包装机械的核心部件为电子秤。传统的种子配料包装系统是单一的手动操作,系统稳定差、精度低,不能确保产品质量,生产效率低。基于模糊PID与PLC控制的配料包装系统,采用微机监控称重配料全过程,并自动进行称量误差补偿,操作人员通过人机操作界面进行系统参数设置、修改工艺设定值,当设备出现故障时及时报警,并自动切断设备电源,减少了称重原料消耗,确保了称量精度和产品质量、实现了管理科学规范化、生产过程自动化,提高了生产效率。
2. 系统功能与结构框图
自动配料包装系统是利用PLC控制变频调速进料机构,配合微机软件控制,实现对不同类型的种子进行输送、分类、分选、装袋、称重、包装、生产数据管理等功能的自动化生产线。为提高称量精度,通过网络实现多个称量系统集中控制。
2.1. 系统功能要求
为确保计量精度,在称重槽下安装T-BX应变式计量传感器,并将数据以RS232方式传送到工业计算机PLC中。系统停机时对称重槽零位监视,并进行人工检零;连续配、送料时系统对称重槽零位自检修正。为加快称量速度,确保了称量精度,系统给料分粗给料和细给料两个阶段。第一阶段为粗给料,进料快,时间短,为额定量的90%至95%。第二阶段为细给料,为额定量的5%至10%。配料过程中,闸门故障造成堵塞时,系统自停报警,并做出相应处理。加料过程结束,放料气动阀开启,开始放料。物料在重力作用下自然流出。当系统检测到称重槽重量为零位时,关闭放料气动阀,放料结束。
2.2. 系统方框图
系统主要由工业计算机、控制台、变频器、A/D转换、电子秤和料斗六部分组成。系统总体结构如图1所示。
工业计算机和变频器是系统的核心,在一个称重循环过程完成后, 关闭称斗,迅速排空料斗内附着物料,然后测皮重补偿称量误差,进入下一个称重循环 [2] 。
2.3. 系统的功能
(1) 自动控制装袋重量与包装;(2) 自检称斗皮重补偿称量误差;(3) 故障自检报警。系统具有称量范围大、速度快、精度高的特点。通过参数设置可实现每分钟6至8包,10到50 Kg的称重量,动、静态精度 ≥ 0.2%。
3. 系统硬件设计
称重传感器是系统关键部分,选型、连接方式和控制方式是提高系统精度的前提 [3] ,设计思路如下。
3.1. 传感器电路设计
传感器是将质量信号转换为电信号输出的测量装置,是称量控制系统的核心。根据自动配料包装控制系统的工作环境,为实现系统功能及控制要求,选用XTR115为核心的半导体应变式传感器,其内部结构图如图2所示。主要有应变桥构成检测电路、TL061运算放大器、XTR115精密电流变送器等组成。称重传感器主要由弹性体、电阻应变片、电缆线组成惠斯通应变桥。当弹性体荷载发生形变时,便输出物质重量的电信号 [4] 。图2中,把电阻应变片因荷载产生的电阻变化,由应变桥构成检测电路转为物质重量电压信号,经TL061放大后输送到XTR115精密电流变送器的第5脚,将电压信号转换为电流信号由第4脚输出。
3.2. PLC控制电路设计
系统选用型号为FXIN-40MR的PLC为核心控制器,结合3A模块的输入通道实现称重信号转换处理,处理后的信号再经3A的输出通道控制相应部件动作。I/O分配表如表1所示,I/O接线图如图3所示。
3.3. PLC与称重传感器的连接
称重传感器经量纲转换后通过A/D采样送入PLC进行运算处理,信息流向如图4所示。
4. 控制算法的实现
为了确保称量精度,提高生产效率,将配料分粗配料和精配料两个阶段 [5] 。粗配料流量大速度快,精配料速度慢。系统进料精度的高低关键是控制粗、精配料的速度和找到精、粗配料过程的切换点合理解决精度与速度的矛盾关系。本系统采用模糊控制技术,对粗、精配料的初始阶段实施多变量动态控制;采用PID算法控制实现称量误差带的精确静态控制与补偿。模糊控制的关键是选择合适模糊控制器与模糊规则建立。
本系统模糊控制器由四部分组成,构成双输入单输出模型。框图如图5所示。控制器有三个变量:
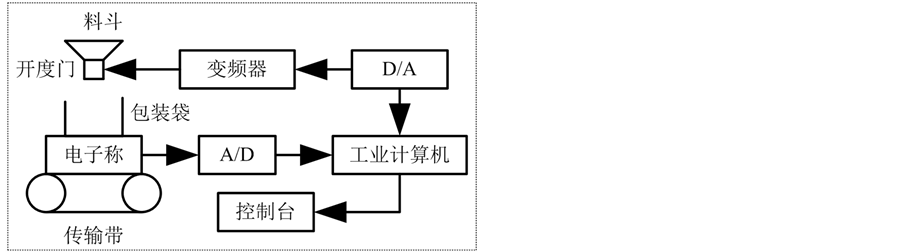
Figure 1. System overall structure diagram
图1. 系统总体结构框图
第一输入变量是物料流量偏差e,和偏差变化率ec。第二个输入变量是期望值y,用于控制配料斗不同高度落差产生的超调量;第三个变量为输出变量u。将e、y、u模糊化后,得E、Y和U信号。
根据如图6隶属度函数所示,在X、Y、Z上的模糊子集{EI,YJ,UIJ},模糊关系R = UIJ (EI × YJ) × UIJ和知条件EI和YJ,进行模糊合成计算与决策即Uij。
由模糊合成推理规则,得出模糊集合U满足U = R × (E × Y)模糊关系,模糊控制规则见表2。
本系统因系统内存不足,所以选用增量式PID控制,采用增量公式计算如下:

Figure 5. Block diagram of fuzzy PID controller
图5. 模糊PID控制器框图
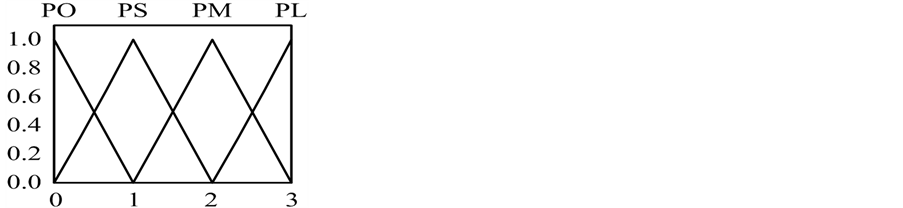
Figure 6. Membership function definition rule
图6. 隶属度函数定义规则
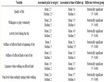
Table 1. System I/O distribution table
表1. 系统I/O分配表
表2. 模糊控制规则表
注:※表示该状态不存在,*表示PID控制。
(3)
式中,ΔP(k)为k时刻控制增量,e(k)、e(k − 1)、e(k − 2)分别为第k、k − 1、k − 2时刻采样偏差值。K1、K2、K3为经验系数,需现场调试修改。为保持系统压力稳定,采用压力补偿方法。即当压力下降时,U(k)减小,偏差e(k)增大,电动机工作频率升高、转速加快、压力上升 [6] 。输入、输出偏差信号离散化后,系统动态性能下降,抗干扰能力变差,需依据偏差大小及变化率,利用数字滤波和自动调节PID的比例系数KP、积分常数KI和微分常数KD的方法来抑制干扰,增强系统的实时控制能力。
5. 系统的软件设计
系统总体流程图
由I/O地址分配表可知,该系统有启动、停机、斗门状态、夹袋夹紧和气源压力开关5个检测信号输入,粗进料、细进料、卸料、夹袋、称重、运行标志、报警7个控制信号输出。根据输入输出信号的数量,选择型号为FXIN-40MR三菱PLC可编程序控制器;选用XSB5高精度称重传感显示控制仪;构成自动化程度高的称量控制系统。用接近开关检测称重斗门关闭和夹袋夹紧信号。料门缓冲、称重斗门、夹袋,动作,由电磁阀控制相应气缸运动实现。系统总体流程如图7所示。只要按下启动按钮,系统启动自动快慢进料、称重、装袋、包装、计数等动作过程。通过PLC精准控制双作用气缸行程速度,结合手动调节进料门的开度大小完成快慢进料,提高了称重速度和精度。
C语言模糊控制程序代码如下:
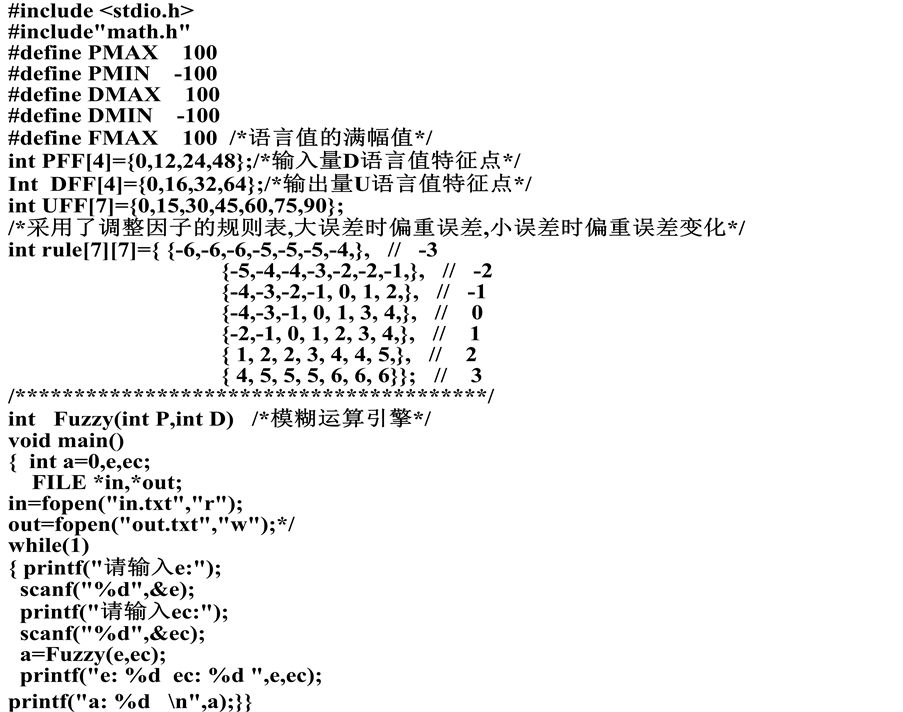
6. 系统仿真与运行测试
将模糊PID控制与常规PID控制进行软件仿真运行试验 [7] 。运行情况如图8所示。
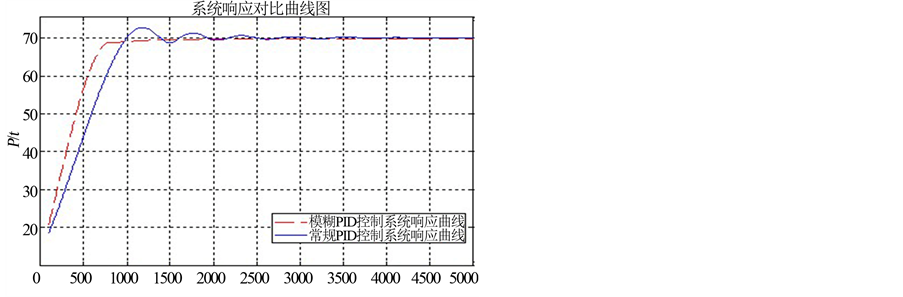
Figure 8. Comparison of response curves between fuzzy PID and conventional PID control
图8. 模糊PID与常规PID控制响应曲线比较
响应曲线结果表明,模糊PID控制比常规PID控制超调量低,大大改善系统动、静态性能。本系统自2013年8月应用于我院种业有限公司的包装机中至今,运行效果好,性能稳定。
7. 结束语
模糊PID控制与PLC控制有效结合,匹配专用高精度压力称重传感器构成自动配料称量包装控制系统,自动化程度高,实现了自动配料称量包装过程的动、静态精准控制,确保了称量精度和产品质量,提高了生产效率。实践证明该系统运行性能稳定、可靠,效果好,具有较高推广价值。