1. 引言
齿轮泵是一种广泛应用于各种液压系统中的动力元件,其主要优点是成本低、结构设计紧凑、体积小、重量较轻,且自吸能力好,运行稳定可靠,可适应多种工作场景 [1] ,但齿轮泵也有明显的缺点,即存在着困油问题。同时,随着社会发展,齿轮泵的工作场景也变得更加复杂化,这也就更加要求齿轮泵向着高压高转速的方向发展,但高压高转速势必会产生更为严重的困油问题 [2] 。目前,解决齿轮泵困油现象的措施主要从齿轮泵侧隙和间隙的改变、困油模型的完善以及卸荷槽的优化等方面着手,本文将对国内外的相关研究进行综述,着重对困油模型和卸荷槽进行分析优化,期望可以为以后齿轮泵困油现象的研究提供参考。
2. 外啮合齿轮泵困油现象产生原因
在实际生产工作中,为了保证齿轮泵能供正常平稳的旋转以及供油,并减小装配难度,通常在设计时齿轮啮合的重合度会大于1,即,当一对齿轮进入啮合状态时,有另一对齿轮依旧处于啮合状态,此时两侧的端板与这两对齿轮之间就形成了一个不与高低压油区相同的密闭容积,容积的大小会随着齿轮的转动而发生周期性变化,由高压油区啮入的齿所形成的容积快速变小,由于油液的可压缩性小进而形成超高压,使齿轮啮合的阻力增大,侧板压力变大,产生冲击载荷,对齿转过中点线后容积快速变大形成气穴,产生气蚀和噪音、振动,此即为齿轮泵的困油现象 [3] 。
3. 外啮合齿轮泵的数学困油模型研究
最初,经国内外多名学者的研究表明 [4] ,外啮合齿轮泵困油空间内的压力变化主要与困油容积的变化以及困油容积内的泄漏量有关,并建立困油模型如式(1)所示
(1)
其中,
是困油压力对时间的变化率;
是困油容积对时间的变化率,也叫困油流量,是造成困油压力的主要原因;K是体积弹性模量;Q是困油容积内的泄漏量,可以对困油压力进行缓解。困油模型式(1)求解的关键是对于P、V、K基本量的计算,针对此,目前国内外的学者都进行了一定的相关研究试验 [5] 。
以式(2)所示微分方程组,在式(1)困油模型的基础上,分别对齿轮泵主从动轮两侧的困油区的困油压力进行了仿真实验,但该式(1)模型考虑简单,困油容积内的泄露仅涉及了侧隙的泄露量,也未考虑液压油中的气体含量对
体积弹性模量的影响,仿真结果如图1,结果并不理想,应考虑多因素的影响,提高模型的可信性 [6] [7] 。
(2)
公式(4)中,
为困油容积内的体积弹性模量,
为侧隙流量,
、
为主、从动轮侧的卸荷流量,
、
为主、从动轮侧的困油容积。
利用质量方程式(3)对齿轮泵进行仿真实验,结果显示,液压油中的气体含量对仿真实验有较大的影响,Borghi也对气液两相进行仿真实验,得到基本一致的结果。由此可见,气穴现象产生的气体冲击对困油现象有较大的影响,式(1)的数学模型应考虑此因素 [8] [9] 。
(3)
式(3)中,
为困油容积的压力,
困油容积的泄漏量,s为啮合半径,
为齿轮主动轮的角速度。
齿轮泵的困油现象受卸荷槽和侧隙的影响较大,侧隙主要影响着困油模型中侧隙泄露量的多少,卸荷槽的位置会使齿轮泵齿面的油压分布发生改变,而两者又是齿轮泵的重要动力学参数,因此,需要将齿轮泵的侧隙、卸荷槽与其动力学特性相结合,建立具有耦合性的困油模型 [10] 。
图2为齿轮困油过程的两个特殊位置,以此为研究对象,进行困油特性与动力学特性耦合的动态困油模型分析。
(a)
(b)
Figure 2. Mesh diagram of gear pump trapped oil process
图2. 齿轮泵困油过程啮合图
采用式(1)的困油模型,以位置变量s来替换原式中的时间变量t,则两困油区
、
可表示为 [11] :
(4)
式(4)中,
为齿轮基圆半径、
为角速度,
、
、
和
、
、
分别为困油区域1、2的体积、压力、弹性模量。
综合考虑齿轮困油区域的泄露流量,可得出 [12] :
(5)
式(5)中,
、
为困油区域1、2的总泄漏量,
、
、
、
和
、
、
、
分别为困油区域1、2的侧隙泄漏量、卸荷流量、轴向泄漏量、啮合流量。
针对齿轮扭转的振动位移,其动力模型可表示为 [13] [14] :
(6)
式(6)中,X为在初始侧隙下的振动位移,可进行间隙的二次分配,
为从动轮传动效率,
、
分别为主从动轮的转动惯量,
为从动轮的转矩,
为线性的阻尼因子,
为齿轮副的整体刚度。
此数学模型可进行动态分配,对此的求解依赖于动态间隙的计算 [15] [16] ,因此,将式(4)和式(6)进行耦合求解,可得:
(7)
结合文献中分析,需要考虑液压油中的气体含量 [17] ,可由液压弹簧效应得出体积弹性模量
、
:
(8)
式(8)中,
为油液的体积弹性模量,
为等熵多变指数,
中
取1.4 (空气) [18] ,
、
为液压油中气体所占体积分数,可有齿轮泵进口油所含气体的体积分数
得到,如式(7)所示。
(9)
对于式(9),
为进油口压力。其中,在考虑齿轮泵高转速产生的离心力时,
可对含气体积百分比进行修正 [19] [20] 。
式(7)考虑了齿轮泵转速、含气比、齿侧间隙、啮合间隙、齿轮振动等多个因素的动态困油数学模型,可用龙格—库塔法对其与静态模型进行仿真运算,可对比分析得出:
1) 齿轮泵进油口含气比高,是造成困油区域膨胀阶段处于低压的主要原因,过小的侧隙和过大的进油口压力会加剧泵体的振动,实际生产中应及时避免;
2) 困油容积与泄露流量是影响齿轮泵困油压力的重要因素,应采取措施减小前者增加后者,同时不能忽视啮合泄漏量以及轴向流量的影响;
3) 较小的齿轮转速、齿数、压力角、齿宽以及模数取值,对缓解困油现象更由帮助,而较大的含气比、侧隙、困油容积以及变位系数,对缓解困油现象更有帮助,应将此应用于实践生产中。
4. 外啮合轮泵的卸荷槽优化研究
困油现象的产生是齿轮啮合时将液压用密封于封闭腔内,随着封闭腔容积的不断变化,周期性的产生高压冲击以及低压空穴问题,这既对齿轮的表面材料产生了破坏,也会降低齿轮泵自身的容积效率。为了解决这个问题,卸荷槽设计与优化无疑是重中之重 [21] [22] 。
传统的卸荷槽主要由矩形卸荷槽和圆形卸荷槽,如图3所示,其中又可以分为对称矩形或圆形卸荷槽、不对称矩形或圆形卸荷槽、单个圆形卸荷槽等多种卸荷槽,其主要参数的计算方法已经较为普及,可以满足于多种生产场景。
(a)
(b)
Figure 3. Schematic diagram of rectangular and circular unloading slots
图3. 矩形、圆形卸荷槽示意图
李玉龙 [23] ,通过对圆形、矩形卸荷槽进行卸荷面积的准确计算,并进行困油压力的仿真运算,得出结论:对于小侧隙大卸荷槽间距的齿轮泵,应选择矩形卸荷槽,可以增大卸荷面积;反之,采用圆形卸荷槽,可以降低维修成本。这一结论,为工程实践中卸荷槽的开设提供了科学依据。
除了在齿轮泵两侧盖板上开设卸荷槽外,臧克江 [24] 提出了一种开设在齿轮非工作齿廓面上的新式卸荷降压槽,如图4所示,且其开设方式不会降低齿轮工作齿廓面的强度,以及齿轮运转的稳定性。

Figure 4. Schematic diagram of the new unloading and pressure reduction tank
图4. 新式卸荷降压槽示意图
以CB100型齿轮泵为研究对象,对其开设卸荷降压槽前后进行对比分析。

Figure 5. Comparison of pressure in oil trapped areas
图5. 困油区域压力对比图
如图5所示,1为未开设卸荷降压槽的齿轮泵的压力曲线,2为开设卸荷降压槽的齿轮泵的压力曲线,可清晰看出,卸荷降压槽虽不能完全解决困油压力问题,但是对困油问题具有较好的缓解作用,适合与小侧隙、无侧隙齿轮泵中的卸荷槽进行搭配使用。
目前,在卸荷槽的设计方面,依旧是对于齿轮两侧盖板上的卸荷槽进行创新研发,且卸荷槽的形状可开始趋于多样化,如图6所示,为一梯形卸荷槽的设计 [25] 。

Figure 6. Schematic diagram of trapezoidal unloading groove structure
图6. 梯形卸荷槽结构示意图
基于CFD流体仿真软件,在不同工况下,如表1计算工况,对试验齿轮泵进行流体仿真分析,对照组为该实验泵原耳形卸荷槽。对图7不同工况下监测点压力与出油口流量脉动系数降低数值比较图,进行分析可得,在齿轮泵处于1000~4000 r/min时,梯形卸荷槽能够更好的降低齿轮泵困油的压力峰值,降低流量脉动,是对齿轮泵卸荷槽设计的一种创新思路 [26] 。
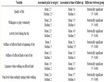
Table 1. Calculation of working conditions
表1. 计算工况

Figure 7. Comparison of the reduction values of pulsation coefficient under different operating conditions
图7. 不同工况下脉动系数降低数值比较图
5. 结论
研究以上文献可以看出,在齿轮泵的困油模型方面,从最开始只简单考虑侧隙泄漏量的数学模型到开始针对齿轮泵动力学特性的力学模型 [27] ,再到现在能够反应齿轮泵动力学特性与困油现象耦合关系的困油模型,其发展历程是缓慢且上升的,目前已处于一个较为完善的阶段 [28] [29] ;而在卸荷槽方面,基于困油模型的逐渐完善,目前也已经从较为传统的矩形卸荷槽、圆形卸荷槽,发展为组合式卸荷槽以及异形卸荷槽,在保证卸荷槽功能的同时也要使其便于加工、降低成本 [30] 。
综合目前对于齿轮泵困油现象的研究进展,可以通过以下几个方面进行进一步的研究:
1) 模型自由度,建议采用6个自由度的弹性力学模型,基于此进行深入研究 [31] ;
2) 齿轮副对困油的影响,目前困油模型的建立是基于齿轮副无受载变形、自身振动以及生产安装误差等的假设下 [32] ,而事实上齿轮的振动等因素不可避免会引起困油容积、齿轮啮合等几何失真,至于具体如何影响可以作继续的深入研究;
3) 进一步研究齿轮副综合刚度问题,对于综合刚度的计算,目前都始于接触刚度和油膜挤压刚度,且只计入主、从动轮面的逼近接触时的油膜挤压刚度,但具体困油现象与综合刚度之间的关系,缺乏相关的研究,建议对此进行相关研究 [33] ;
4) 在考虑齿面润滑、卸荷槽等因素的影响下,对齿面啮合力矩进行实际测量的深入研究。
NOTES
*通讯作者。